A flange is a metal ring welded to the ends of a pipe and allows a rigid connection between pipes or between a pipe and a device. It has several holes parallel to the center of the tube, which can accept bolts for tightening. It is mostly used as an alternative to the welded connection, for obvious practical reasons.
The key parameters of a flange are:
- The nominal size, i.e. the size of the flange hole, which must match the size of the pipe hole;
- The nominal pressure, which refers to the allowable internal pressure, expressed in bar, for a temperature of 20 °C.
“There are different types of flanges: standard and special.”
There are different types of flanges on the market, largely used in the various industrial, hydraulic, agricultural, etc. sectors, and are divided into standard and special types.
The first type of standard flange is the welding neck flange, which is characterized by a conical hub to be welded onto the tube. This type of flange is typically used in applications that require high pressure, high or low temperatures, and a uniform fluid flow. In fact, the diameter of the flange is the same as that of the pipe, which leads to the absence of pressure losses and therefore prevents turbulence and corrosion/erosion near the flanged joints.
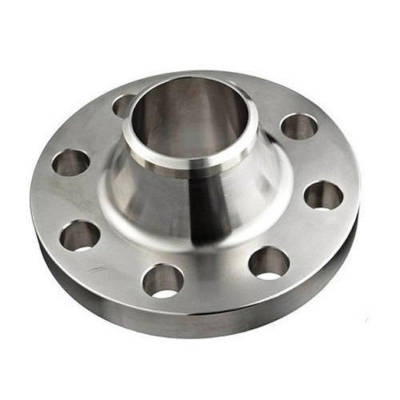
The conical hub also allows for uniform distribution of the mechanical stresses between the tube and the flange.
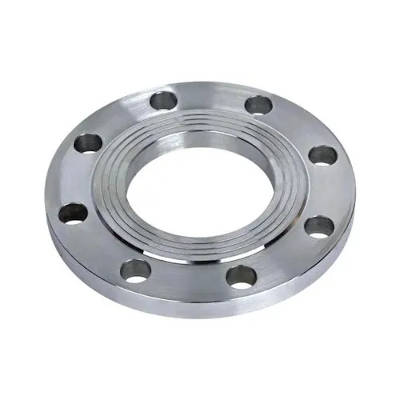
A second very common type of flange is the slip-on for welding flange, which has a diameter slightly greater than the external diameter of the pipe, which runs inside it and is welded to it using two welds: one inside and one outside the cavity of the flange. Compared to the welding neck flange, the slip-on flange is a little more fragile due to the absence of the conical hub and the presence of two welding areas instead of one.
Another standard flange is the socket weld flange, which is very similar to the slip-on flange with the difference that it has a step inside against which the pipe, once slid into the flange, comes into contact, so it is necessary to execute only one weld on the external side of the flange, unlike the two welds that are necessary for the slip-on flange.
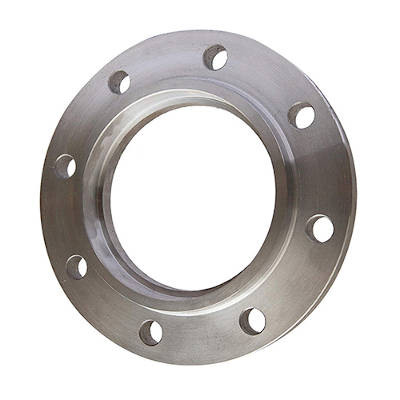
Socket weld flanges require to leave a space of at least 1.6 mm between the step and the pipe before welding, which is necessary to allow the pipe to be positioned correctly inside the socket after the weld has solidified.
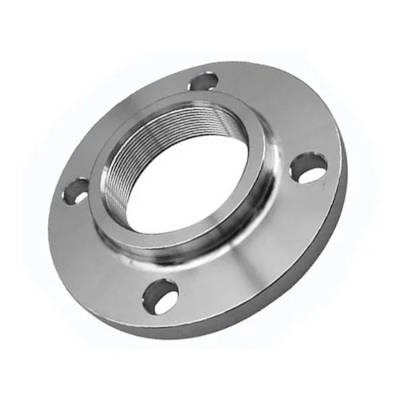
Very common for low pressure and low temperature applications is the threaded flange, which has a thread inside and which therefore must be screwed to the pipe, without welding (although in some cases small welds are made to increase the resistance of the connection). Threaded flanges are mandatory for use in explosive areas, such as petrol stations and plants, because the use of welded connections is dangerous.
The last type of flange that we want to describe is the blind flange, which, unlike those seen so far, does not have a central hole and is typically used to close or seal a pipe, a valve or other devices to block the flow of fluid. Blind flanges must withstand considerable mechanical stress due to the pressure and tightening forces required. They must also allow an easy access to the pipe, therefore being easily unscrewed to allow the operator to carry out maintenance activities.
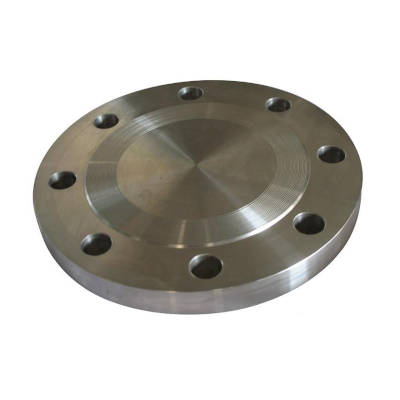
These are the most common types of flanges used in the industrial and hydraulic fields, however there are many other more particular ones, which may be discussed in depth in a future article.
At Irritecnica we pay much attention to the choice and sizing of the flanges for our flanged pipes, in order to optimize the pipes for the required application, both in terms of pressures and temperatures involved. Contact us for more information or visit our websites Irritecnica.it, Tubiflangiati.it and Flangedpipes.com.